The sizing of electrical cables is a critical aspect of electrical system design and installation, directly impacting safety, reliability, and efficiency. Selecting the appropriate conductor size requires consideration of several factors, including the rated current of the load, permissible voltage drop, operating temperature, installation method, and environmental conditions.
Proper cable sizing helps prevent overheating, minimizes energy losses, and reduces the risk of faults or fire hazards. Moreover, it must comply with relevant technical and safety standards, such as the National Electrical Code (NEC) in the United States, BS 7671 (IET Wiring Regulations) in the United Kingdom, AS/NZS 3008 in Australia, and IEC 60364 internationally, which is commonly followed in India and other regions. Utilizing calculation software or reference tables allows engineers to determine the optimal cable size, ensuring system continuity and protection for both people and equipment.
Recommended Wire Size: –
Reference: –
Key Electrical Wire Sizing Standards
Proper sizing of electrical cables is crucial to ensure the safety and efficiency of electrical installations. Various countries have established specific standards to guide this process:
- United States: The National Electrical Code (NEC), also known as NFPA 70, provides comprehensive guidelines for electrical installations, including cable sizing. It defines parameters such as current-carrying capacity, voltage drop, and installation conditions.
- United Kingdom: The BS 7671, commonly referred to as the IET Wiring Regulations, outlines the requirements for electrical installations in the UK. It covers aspects like conductor sizing, protection against overcurrent, and methods of installation.
- India: The Indian Electricity Rules and standards set by the Bureau of Indian Standards (BIS), such as IS 732, provide guidelines for electrical wiring installations, including cable sizing, safety measures, and installation practices.
- Australia: The AS/NZS 3000, known as the Australian/New Zealand Wiring Rules, specifies the standards for electrical installations, including the selection and sizing of cables, ensuring safety and compliance with performance requirements.
Adherence to these standards is essential for professionals to design and maintain electrical systems that are safe, efficient, and compliant with regional regulations.
Essential Electrical Wire Sizing Terminology
To effectively understand wire sizing, it is essential to understand some key electrical quantities:
- Electrical Resistance (Ohm): The resistance of the conductor and the overall impedance influence both the voltage drop and the power losses. For long lines or with high loads, it is important to consider these parameters to avoid energy waste. Copper has a lower resistivity than aluminum, which indicates better conductivity.
- Voltage drop (ΔV): The reduction in voltage along the cable due to electrical resistance. It must be kept within limits established by regulations (generally not more than 4-5% of the nominal voltage). Excessive voltage drop may compromise the correct operation of electrical equipment.
- Rated Current (Amperes): The maximum amount of current a wire can carry continuously without exceeding its rated temperature, measured in Amperes (A).
- Circular mils (cmil): A U.S. unit of area used to quantify the cross-sectional area of wires. 1 cmil is equal to the area of a circle with a diameter of 0.001 inch.
AWG to Metric Wire Size Conversion Chart
Converting American Wire Gauge (AWG) to Square Millimeters (mm²): This table provides approximate conversions. For precise values, refer to comprehensive AWG conversion charts.
Choosing the Right Conductor Material: Copper vs. Aluminum
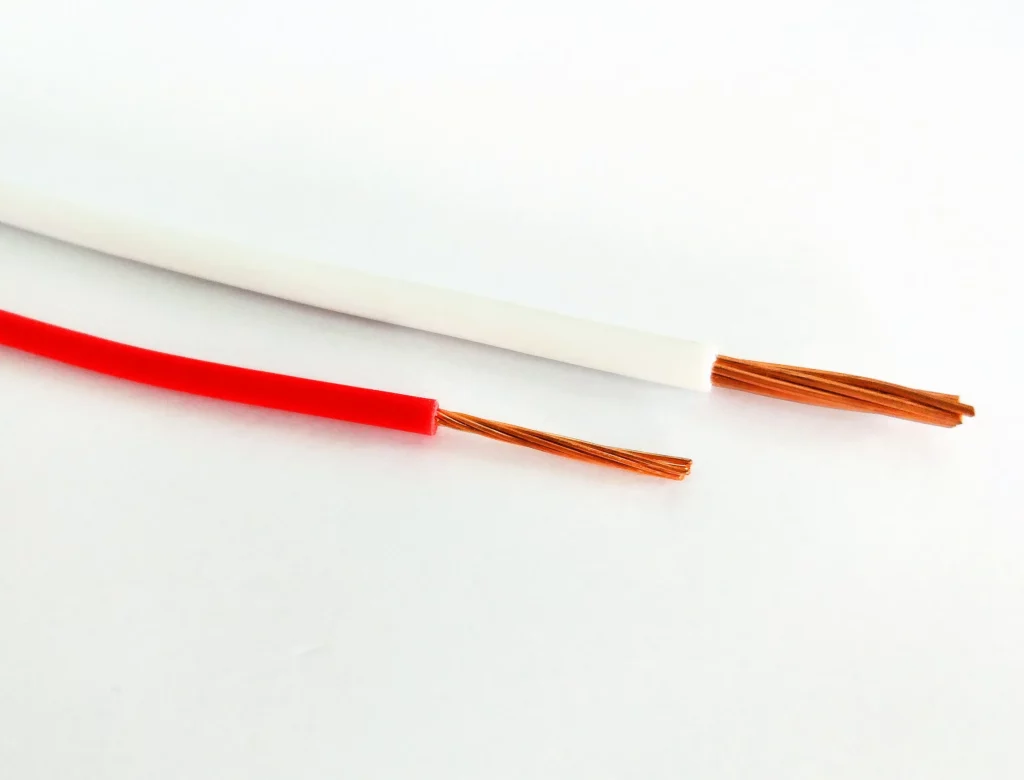
Copper and aluminum are the most common conductive materials.
Copper
Advantages of copper:
- High electrical conductivity: copper has a higher conductivity than aluminum (about 60% more), allowing the use of smaller sections for the same current.
- Greater mechanical resistance: it is more resistant to traction and less prone to breakage or damage during installation.
- Better corrosion resistance: less vulnerable to oxidation than aluminum, ensuring greater durability over time.
- Less susceptible to thermal expansion: reduces the risk of loosening connections in terminals.
Disadvantages of copper:
- Higher Cost: Copper is significantly more expensive than aluminum, both as a material and to install.
- Heavier weight: Being denser, it is heavier, which can make installation difficult in some applications.
Aluminum
Advantages of Aluminum
- Light weight: It is approximately three times lighter than copper, making it easier to handle and install, especially over long distances.
- Lower Cost: It is significantly cheaper than copper, making it advantageous for large installations.
- Good corrosion resistance in dry environments: can be used in some applications without oxidation problems.
Disadvantages of Aluminum:
- Lower electrical conductivity: to carry the same current, aluminum requires a larger cross-section than copper, increasing the space occupied in the conduits.
- Increased thermal expansion: Can cause loosening of electrical connections over time, increasing the risk of overheating or failure.
- Increased sensitivity to oxidation: The oxidation of aluminum creates an insulating layer that can compromise conductivity, requiring specific connectors and maintenance.
- Lower mechanical resistance: it is more fragile than copper and more subject to breakage in the event of bending or excessive tension.
If compact size, high reliability and durability are required, copper is the best choice. If cost and weight are critical factors, especially over long distances, aluminum can be an effective solution, provided that specific precautions are taken to avoid oxidation and overheating problems.
How Cable Length, Temperature, and Current Impact Voltage Drop
Voltage drop is influenced by:
- Cable Length: Longer cables increase resistance and voltage drop.
- Temperature: Higher temperatures increase conductor resistance, leading to greater voltage drop.
- Current: Higher currents result in increased voltage drop.
- Formula for Voltage Drop: ΔV = (I * R * L) / 1000
- Where:
- ΔV = Voltage Drop(V)
- I = Current (A)
- R = Resistance(Ω/km)
- L = Length(m)
- This mean that you can minimize voltage drop by using larger wire sizes or shorter cable lengths.
- Where:
Ensuring Electrical Safety Through Proper Wire Sizing
Improper wire sizing poses significant safety risks:
- Overheating: Undersized wires can overheat, potentially causing fires.
- Equipment Malfunction: Excessive voltage drop can lead to equipment malfunction or failure.
- Short Circuits: Damaged or improperly installed wires can cause short circuits.
- Always follow electrical code requirements and consult with a qualified electrician.
Frequently Asked Questions About Wire Sizing
Why is voltage drop important?
Excessive voltage drop can cause equipment to malfunction, reduce efficiency, and increase energy consumption.
How do I choose the right wire size?
Use a wire sizing calculator or refer to electrical code tables, considering factors like current, voltage, and cable length.
Can I use aluminum instead of copper?
Aluminum is suitable for specific applications but requires larger sizes than copper for the same current capacity. Consult electrical codes and a professional.